Project descriptions
Research at the TAS Functionality Node is focusing on evolving functionality of autonomous systems and how it needs to be specified, designed, verified, validated, curated and regulated to ensure it is safe, reliable, resilient, ethical and trustworthy. This is being achieved through a range of research approaches and case studies. One of the emerging technology being investigated in the TAS project is Soft Robotics
A popular belief in the soft robotics community that soft robots possess ‘intrinsic safety’ features because it is soft. While this is generally true that soft robots can be considered safer from a mechanical point of view, there are several possible safety loopholes that render the robots untrustworthy.
Unlike rigid robotics, where the construction material is considerably robust and is less likely to fail, material failure is a significant safety concern in soft robots. The most common causes of material failure in soft robots are Abrasion, tearing and material degradation. Abrasion, tearing happened when material failed or ruptured due to external influences. This is especially common in Pneumatic actuators. Pneumatic actuators often tend to have a ballooning effect, which is fundamental for actuation. Being enveloped in a covering, the ballooning is usually not directly exposed to the workspace, but it may not always be possible to shield the ballooning area from the work environment. If in direct contact with humans, a tear could cause sudden release of the elastic energy stored in the material, thrusting it to a nearby object. The higher the pressure, the more likely someone will get hurt if they come in close contact. Imagine putting your face next to a big balloon when it burst. Material Degradation causes Structural changes leading to increased stiffness in elastomeric materials. This is especially important in medical procedure (because of change in functionality) – As such, rigorous considerations are required when selecting soft materials in medical procedures.
Another safety loophole is when a soft robot in dynamic mode. Impulse and whiplash effect are the main safety concerns when dealing with soft robot in motion. It is quite straight forward with impulse, for example a soft robot arm moving with high velocity will have a big impulse when it comes in contact with an object. Regarding The whiplash effect, it could happen when a soft robot moves fast or slow. I will go back to the soft robot arm example, now the robot arm moves slowly, however, the velocity of the end effector may increase considerably if the arm encounters an obstacle in the workspace. Imagine a complete soft arm moving from point A to point B. It encounters an obstacle C at the elbow of the arm, Because the arm is soft the part from the elbow the end effector bends backward whilst the part from the base to the elbow keeps moving forward. After the arm move a certain distance the part that bended backwards got freed and quickly bounce back to its original shape due to its elastic energy creating a whiplash effect. The end effector of these arm-like manipulators are equipped with appendages such as grippers or they may be carrying a payload. As such, something soft that has enough mass and move fast can hurt people and cause serious damage. All these examples show that soft robot may not be as trustworthy as people might think. This raises the question of how can we determine what is trustworthiness in soft robots?
One possible area that we can look at in order to answer this question could be in Functionality/DoF. Most conventional soft robots have High dof, high functionality and adaptability but low predictability and low controllability (this means low trustworthiness). In contrast conventional rigid robots have high controllability and predictability (this means high trustworthiness) and limited dof and low adaptability. As such, my hypothesis is that trustworthy soft robots lies in the middle between the 2 extremes and the next step is figure out how to quantify trustworthiness in soft robots.
Below are a list of highlighted works I have done for this project
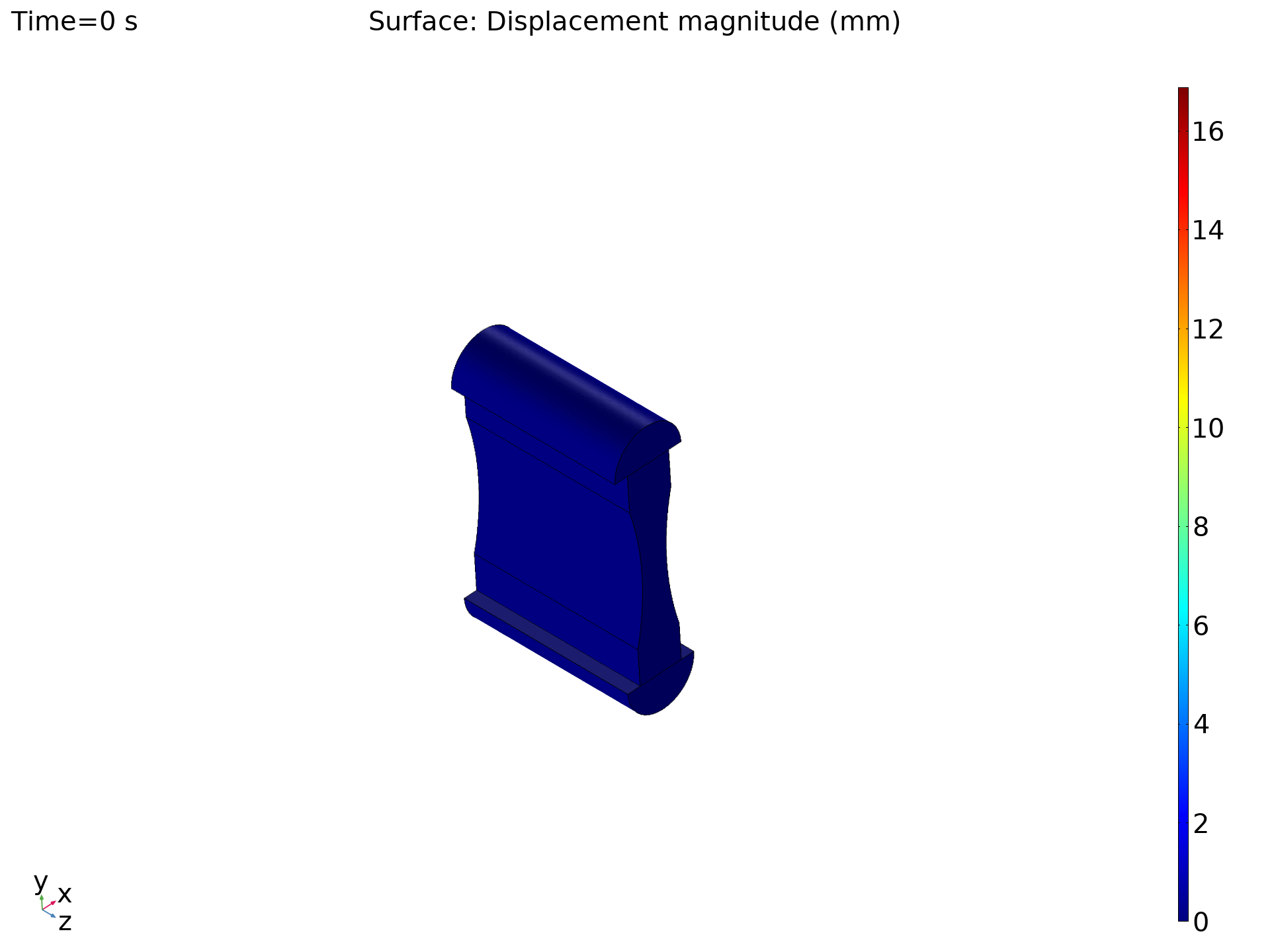
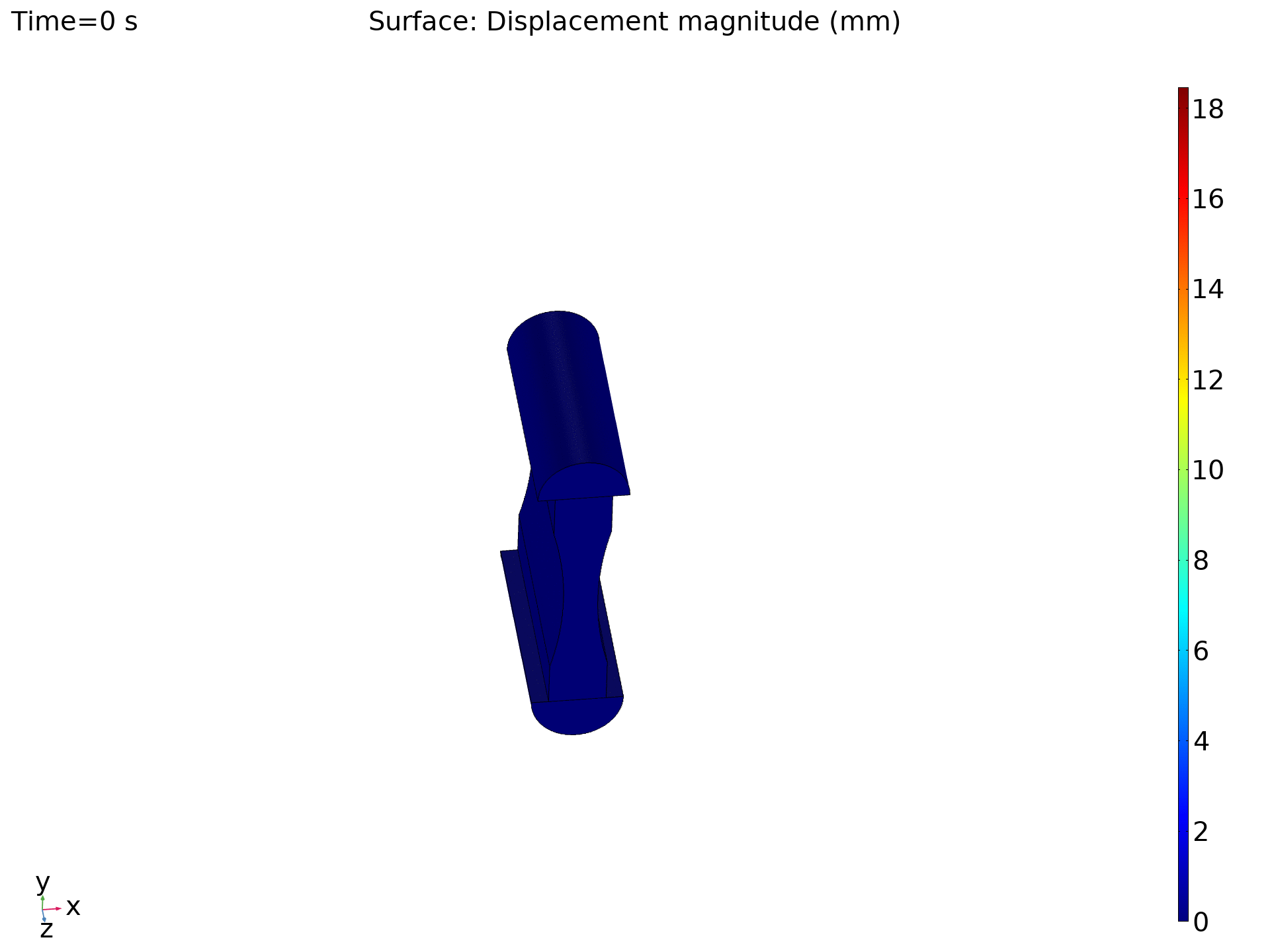
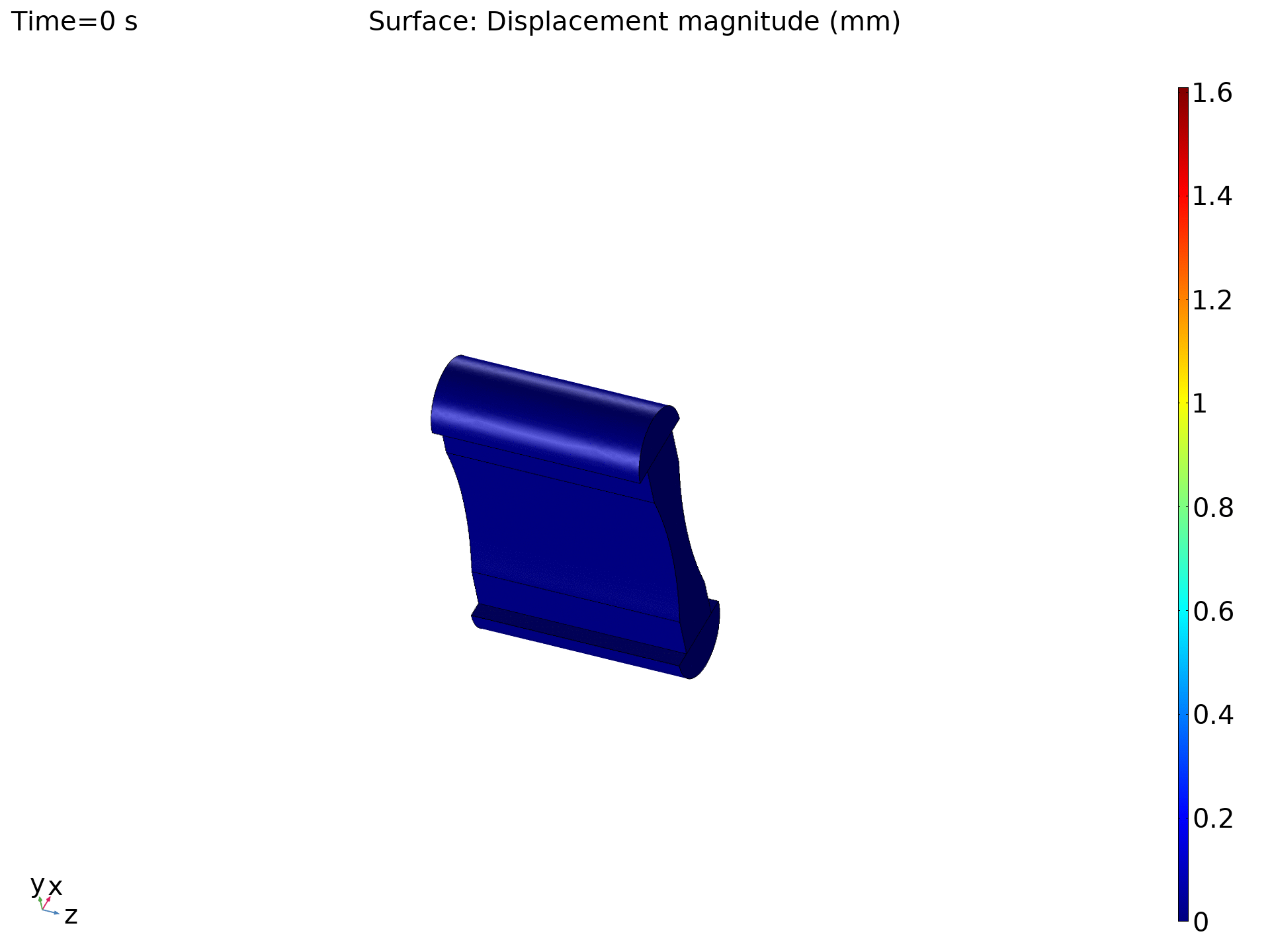
Trustworthy Cubie Gripper
Demonstration at TAS All Hands Meetings, 2022.
The SoftTAS group has been collaborating with Ocado Technology to develop a design framework for trustworthy soft grippers in industrial grocery setting. Ocado's robotic experts are part of the project's industrial advisory board offering top-level context and business challenges for soft robotic grasping. Ocado has provided two UR10 arms to evaluate the performance of trustworthy grippers developed according to the proposed design framework. The SoftTAS group has visited Ocado’s Erith centre to see the systems in use from the storage and retrieval robots to human packing. This helps to put our research work in context and better address the grocery handling challenges. Discussions with senior management and engineers at Ocado have provided an insight into Ocado’s existing system architecture and how our research work could help transform the current systems to be more efficient. We also set up a SoftTAS-Ocado research bay at the BRL dedicated to the development of technologies which could benefit Ocado in the future. This enables further collaboration with Ocado Technology and could result in many exciting research projects with real commercial impacts.
The top row video showcasing the prototype of the cubie gripper gripping different circular shape objects ranging from a smooth bowling ball to a lemon
The bottom row figures are the Comsol simulations of the hinge of the cubie gripper under load in various orientations. The total load applied in all cases is 10N. The middle gif shows the sim behaviour of the hinge under a load applied on the top edge of the hinge (at 0 degree angle) creating a moment around its principal axis. The right gif shows the load applied at the perpendicular top edge of the hinge (at 90 degree angle), the left gif shows the load applied at 45 degree angle.